Fairleads
Article by TMY Editorial Staff. Photos by John Stoudt.
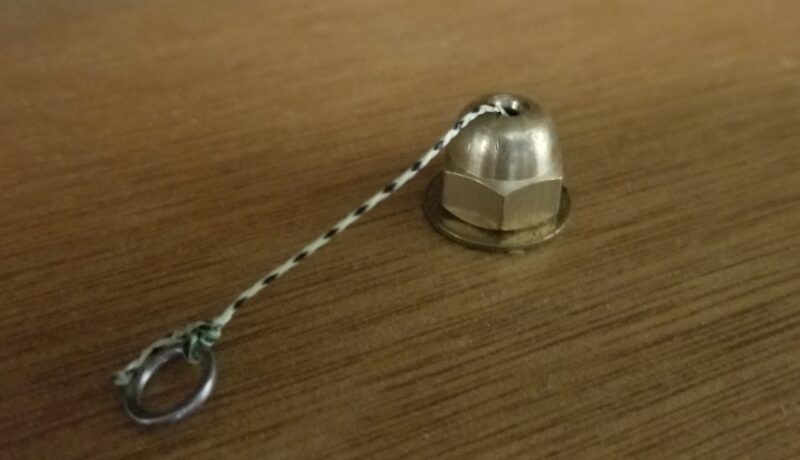
Fairleads for vintage model yachts can be very hard to find,
and if you do find them, they can be a bit pricey, although beautiful.
You can make your own that look good and are functional using hardware store items.
Materials (for one pair)
- Two ¼-20 solid brass acorn nuts
- Four ¼-in brass washers
- Two pieces of ¼-in solid brass all-thread 2 in long
- Two ¼-20 solid brass nuts
- 2 pieces of plywood ¼ in by ¾ in by ¾ in
NOTE: For a silver look, use aluminum instead of brass.
Tools
- Metal lathe or drill press
- 5/64-in and 17/64-in drill bits
- Countersink
- Hack saw
- Centering square
- File and abrasive paper
It is important that you use solid brass or aluminum parts. The brass all-thread must be an alloy with very little silica in it. If the all-thread has silica in it, it will destroy drill bits. We know from experience. You might want to use a brass or aluminum bolt – don’t. They have a high silica content. These are nearly impossible to drill. All-thread can be found online in alloy form that will be very satisfactory and drill relatively easily.
Procedure
- Cut the all-thread long enough to thread into the acorn nut and extend through the deck, king plank, a washer, and far enough to protrude below the deck beams 1/8 to ¼ in.
- Drill the acorn nut and the all-thread. The best way to do this is in a metal lathe. A drill press can also be used with a drill press vice that has a vertical v-slot in it that will hold the pieces plumb for drilling.
- Find the center of the acorn nut (see sidebar). You may have to file off the little tip (residue) on top of the acorn nut.
- Thread the all-thread onto an acorn nut and place the assembly in three jaw chuck on a metal lathe or in the vertical v-slot of a drill press vise.
- Drill a 5/64-in hole through the acorn nut and into the all-thread (just slightly).
- Remove the acorn nut to allow the metal curls to fall away as you drill the all-thread.
- Take your time drilling through the all-thread. Drill in about ⅛-in and back the drill out to allow the drill curls to fall away. Allowing them to build up in the hole helps generate a lot of heat and will pull the temper out of the drill bit, dulling or breaking it. DO NOT OVERHEAT THE DRILL BIT!Listen to the drilling process. The drill will tell you if there is a problem.Repeat the process until you are a little more than half way through the all-thread. Flip the all-thread and continue until the hole is through.
- On both ends of the all-thread and the top of the acorn nut, use a larger drill bit or a countersink and lightly drill a chamfer on the edge of the hole.
- File and sand the rough edges at the ends of the all-thread.
- Drill a 17/64-in hole through the center of the ¼-in plywood. This will be used as a reinforcing piece under the deck.Repeat the process for the other nut and all-thread. With the washers, nuts and all-thread you have a set of fairleads.The fun part is assembling the fairleads on the boat; especially, trying to get your hand into position under the deck to thread the pieces onto the all-thread and tighten the nut.
Finding the Center of Round Material
A center square is a uniquely designed tool that allows you to find the center of a round piece of stock.
Place the center square firmly against the side of the round stock and scribe (draw) a line. Rotate the square about 120° and scribe a second line. Do this a third time. The intersection of these lines is the center of the material.